The Shuliy EPS pelletizer provides an effective solution for grinding styrofoam into high-quality granules, improving foam recycling efficiency. It has a variety of applications and can be used for all sizes of plastic foam recycling and manufacturing factories. Let’s explore the Shuliy EPS Pelletizer for recycling together.
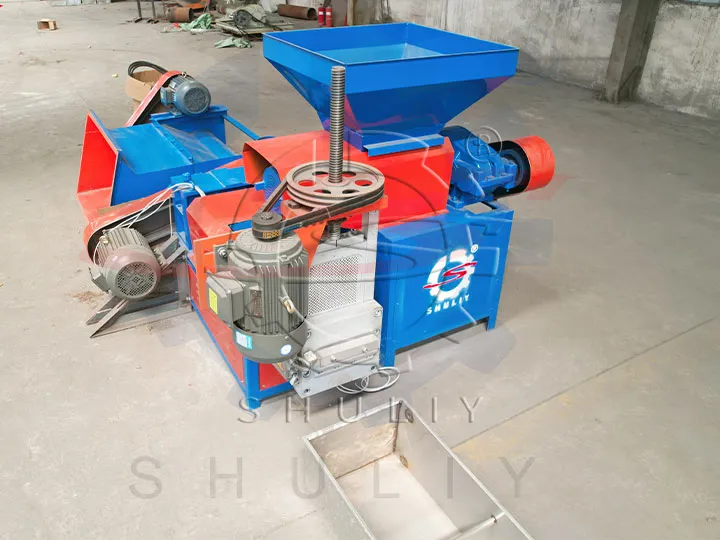
- Capacity: 150~375kg/h
- Raw Materials: EPS foam
- Final Products: EPS granules
- Application: Styrofoam recyclers and manufactures
Why We Choose Shuliy EPS Pelletizing Machines?
- High Efficiency: The EPS granulator can effectively process styrofoam into recycled granules as required at a speed of 150~375kg/h.
- High Quality: Manufactured entirely from stainless steel and subject to rigorous quality sampling, the granulator is very durable, corrosion resistant, and has good quality control.
- Advanced Technology: Automation and double reduction gears for precise control of the machining process. Besides, the screw-melting technology can improve the plastic recycling process.
- Perfect Service: We provide sincere advice and customized machines based on customer’s production needs. In addition, we offer a one-year warranty and operation guides. If you have any questions, please consult us and we’ll try our best to help you.
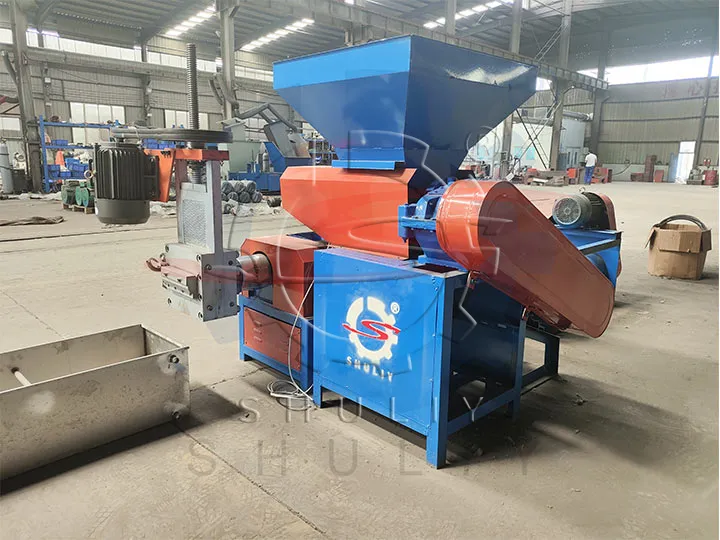
What are the Raw Materials and Final Products of the Foam Grinder?
Raw Materials
The EPS pelletizer is specially designed to transform expanded polystyrene(EPS) into granules. These EPS materials can be collected and divided into the following categories:
Post-consumer EPS Foam:
- Packaging Materials: Courier boxes, electronic product packaging, fruit packaging, etc.
- Building Materials: EPS thermal insulation board, EPS heat insulation board, etc.
- Disposable Tableware: Foam lunch boxes, etc.
Post-industrial EPS Foam:
- Production Edges and Corners: EPS sheet cutting down edges and corners, EPS mold waste, and so on.
- Production Errors: EPS products with irregular shapes and unqualified dimensions.
Final Products
These EPS foam materials are finally processed into uniform granules, which can be recycled and processed into regenerated granules by the foam granulator and used to manufacture new EPS products or other materials.
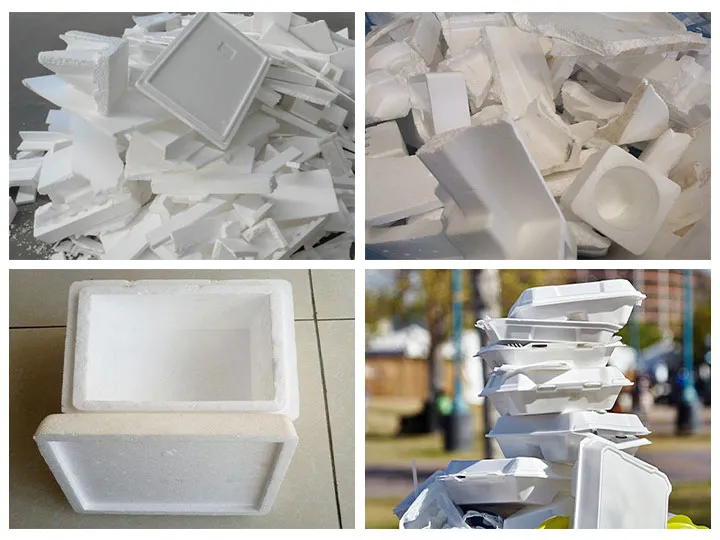
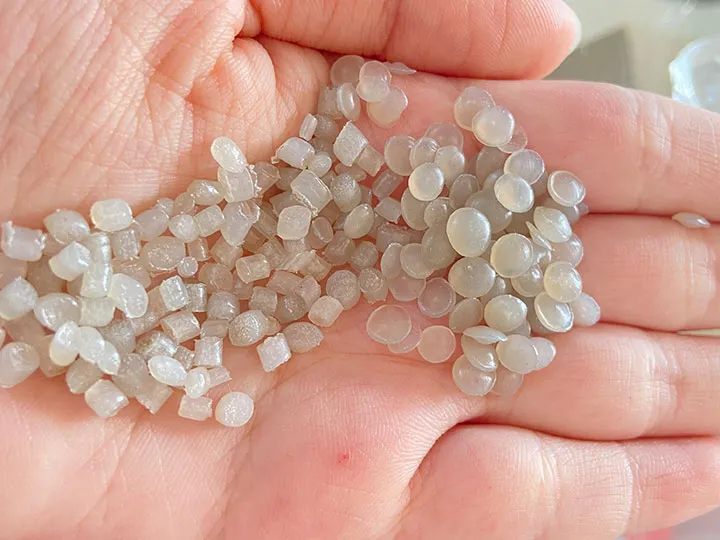
Structure of EPS Foam Pelletizing Machine
EPS foam pelletizing machine is mainly composed of the main machine, auxiliary machine, die head, grinder, and cooling water tank.
- Among them, the host is the core of the EPS pelletizing machine, responsible for processing EPS particles into plastic strips through hot melt, extrusion, and other processes;
- The auxiliary machine with the host provides the necessary auxiliary functions.
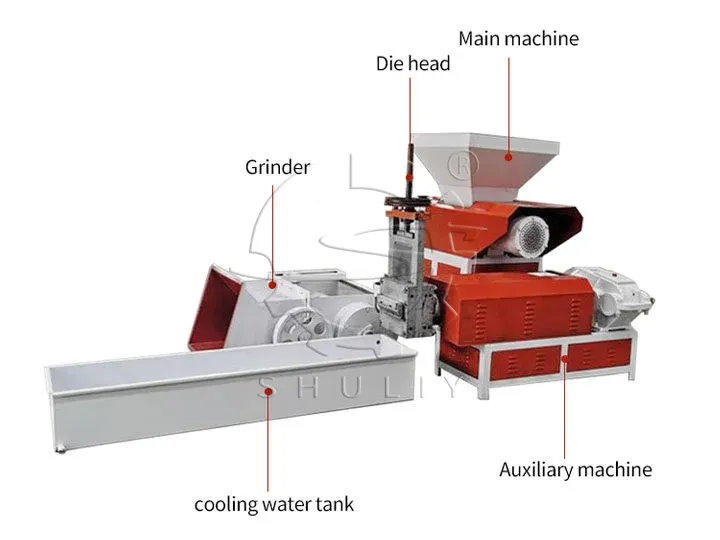
- EPS pelletizer die head is used to form the key components of the particles, its structure and aperture determine the shape and size of the regenerated particles;
- EPS granulator grinder is used to deal with the waste material and the surface treatment of the particles;
- The cooling tank is used to cool down the EPS plastic strips so that it is rapidly to ensure production efficiency and product quality.
How Does the EPS Granulator Work?
EPS pelletizer, as an essential equipment for foam recycling plants, has a simple and efficient workflow.
- Melting: Firstly, the EPS foam is fed into the inlet of the EPS granulator, and the EPS foam is heated to the molten state by the heating system.
- Extrusion and Cooling: Next, a rotating screw pushes the molten EPS foams towards the extrusion outlet. At the extrusion outlet, the molten EPS feedstock is extruded through the die head to form pellets of the desired shape, which are cured after cooling.
- Pelletizing: The entire workflow ensures the production of high-quality EPS pellets by controlling parameters such as heating, extrusion speed, and pressure.
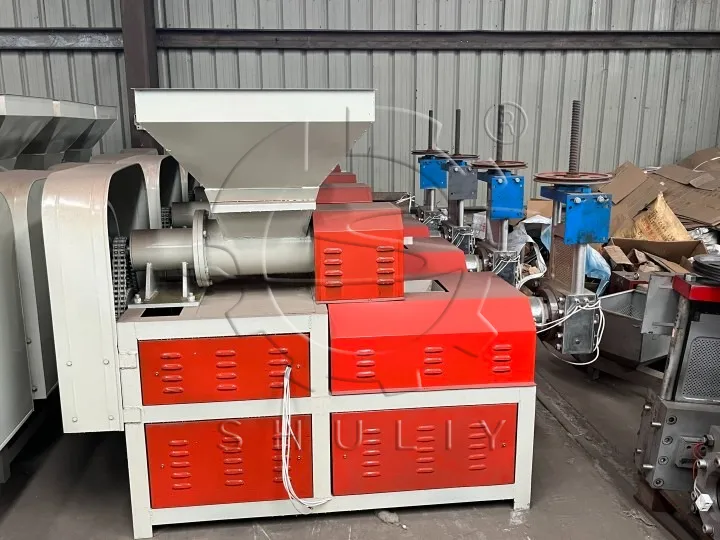
Technical Data of EPS Foam Pelletizing Machine
Some of the hot-selling EPS foam pellets-making machine parameters are as follows. If you’re interested, please feel free to contact us.
Model | SL-220 | SL-270 | SL-320 | SL-350 |
---|---|---|---|---|
Reducer number | double | double | double | double |
Capacity(kg/h) | 150-175 | 200-225 | 275-300 | 325-375 |
Motor Power(Kw) | 15 | 18.5 | 18.5 | 22 |
- There are both double reducers and single reducers equipped with granulators for sale and the above table is about double reducers. If you have other needs, we can also provide customized machines.
- Shuliy EPS foam pellet machines have a great capacity of 150kh/h to 375kg/h. Depending on different production requirements, you can choose various models of pelletizers.
- The power of motors ranges from 15Kw to 22Kw, effectively driving the machine and facilitating the advancement of recycling.
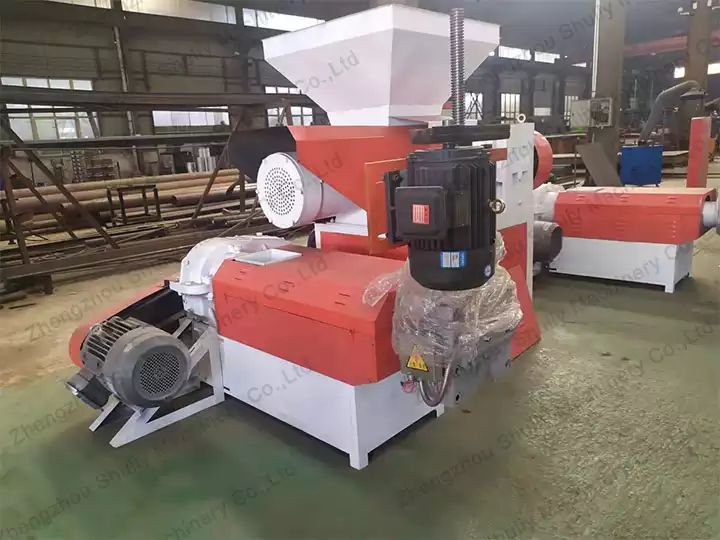
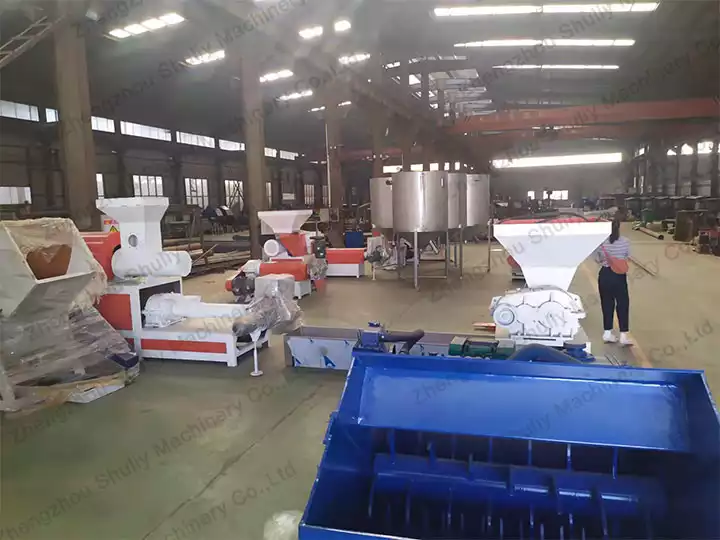
Something You Should Know About Shipment
- The Working Period is about 20~25 days.
- Before shipment, we will inform the customer of the processing progress according to the timings, and send a video of the test machine to ensure that the machine is error-free.
- After receiving the machine, we can offer operation guides, on-site installation service if needed, and a one-year warranty.
Welcome to our factory and we’ll try our best to help you!
One Case of the Shuliy EPS Pelletizer
Our EPS pelletizer has been successfully exported to many countries around the world. Recently, we exported an EPS granulating line to Nigeria. We would like to share a case study and a feedback video from our customer. This customer from Nigeria has improved his EPS and EPE foam recycling business with the help of our foam extruder and is satisfied with our machines. We hope to help more and more plastic recyclers and manufacturers!
EPS Pelletizer for Sale
Do you need an EPS granulator to improve production efficiency? We offer efficient and reliable EPS pelletizers for production lines of all sizes. Our plastic foam extruders utilize advanced technology to efficiently convert EPS scrap into high-quality pellets. Whether you are a startup or a large producer, we can provide you with customized solutions to meet your production needs. Feel free to contact us for more details and to get a quote!
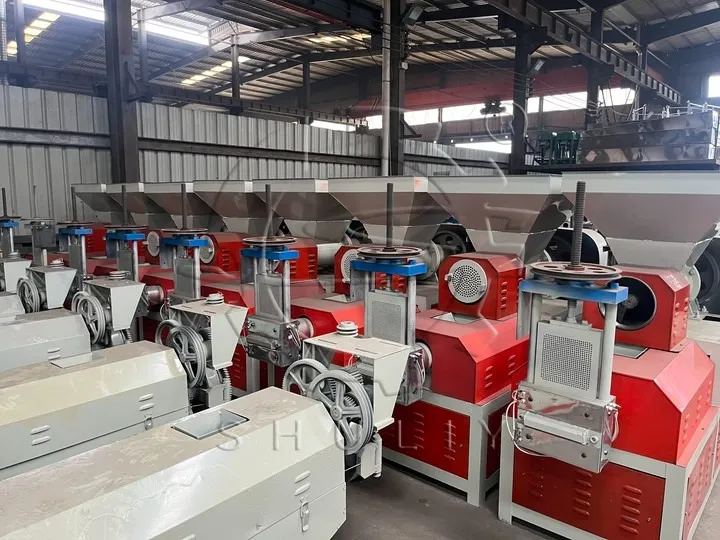