Recently, we successfully sold a 150kg/h EPS styrofoam compactor to Nigeria, which helped the customer improve EPS styrofoam recycling efficiency, reduce operating costs, and increase profitability!
The Background of This Project
Nigeria produces approximately 600,000 tons of waste plastic foam each year, but the local recycling rate is less than 10 percent. Our Nigerian customer is primarily focused on manufacturing recycled EPS pellets. However, producing these pellets is costly due to the large size of the plastic foam and the high storage expenses associated with it. As a solution, he aims to introduce a state-of-the-art EPS styrofoam compactor. This equipment would compress the volume of the raw material, reduce supply chain costs, and help expand his business.
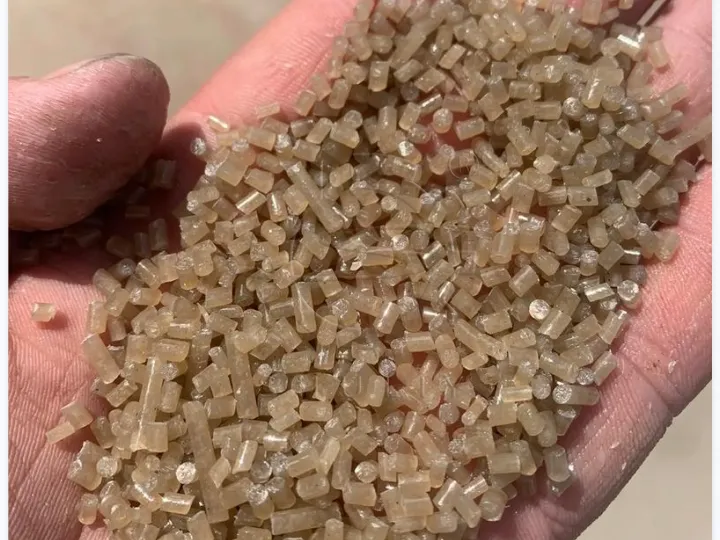
Our Client’s Challenges And Needs
- The collected foams occupy a large amount of storage space, with approximately 70% filled by loose foam, leading to high management and storage costs.
- The loose foam is difficult to process directly, and the recycling efficiency is low, which can’t meet the demand of the styrofoam recycling line.
- Styrofoam recycling machines in Nigeria are outdated, and the cost of European equipment is high, so our customer needs an affordable and durable polystyrene compactor.
- The customer’s factory is located in a place with insufficient electricity, which cannot support the equipment with excessive energy consumption.
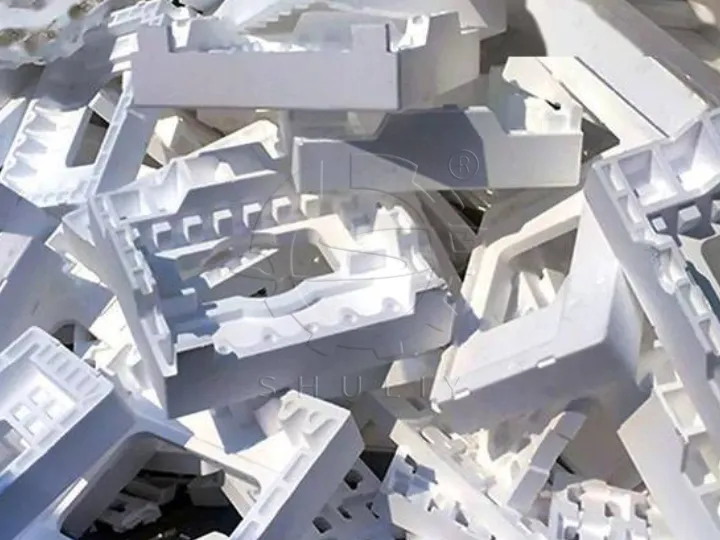
Recycling Solution: 150kg/h EPS Styrofoam Compactor
Understanding the problems and needs faced by the customer, we provided a customized vertical foam compression solution with the following features:
- Wide Application: Processes various plastic foam raw materials, such as EPS, EPE, and XPS, meeting the complex recycling needs of this Nigerian customer.
- High Compression Ratio: The EPS styrofoam compactor can efficiently compress EPS foam up to 1/40 of its volume, reducing storage costs.
- High Productivity: The 150 kg/h EPS styrofoam recycling compactor is tailored to meet the customer’s production requirements and can be integrated with the foam pelletizing system. This compactor efficiently compresses styrofoam into blocks that can be directly crushed and melted. This process minimizes the temporary storage of raw materials and enhances the overall efficiency of styrofoam recycling.
- Low energy consumption: Operates without heating, reducing energy use and making it ideal for areas with limited electricity supply.
- Cost-effective: We offer customized machines with complete core functionality, eliminating unnecessary and expensive configurations, and factory direct sales. This allows customers to get the performance they need at a lower price.
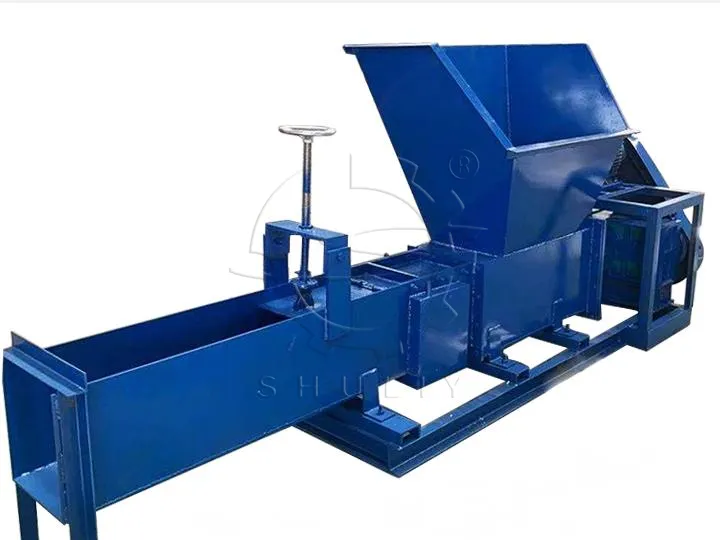
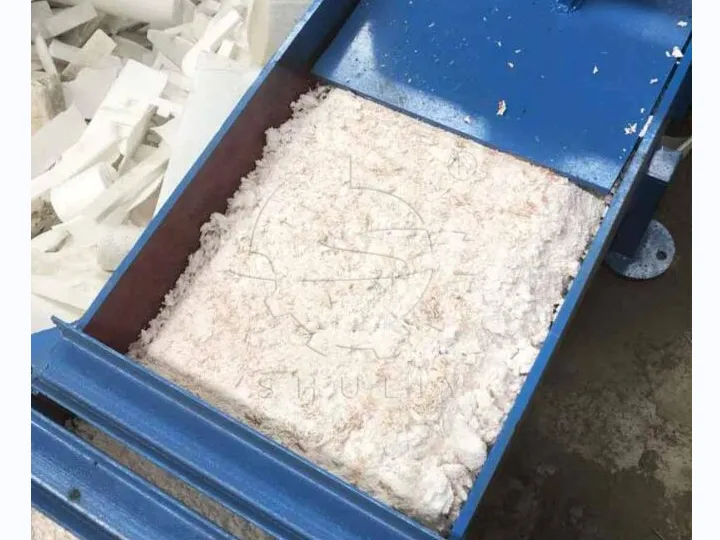
Positive Feedback From Our Nigerian Client
The introduction of the EPS styrofoam compactor has significantly reduced our production costs and improved expanded polystyrene recycling! Now we can finally free up our production budget and storage space to source more low-cost foam from remote locations!
–Ifeanyi Bello, customer in Nigeria
The customer feedback: “Due to limited storage and handling capacity, we previously had to purchase expensive foam raw materials from the surrounding area. Since the EPS styrofoam compactor was installed, storage requirements have been reduced by 80% and line utilization has increased by 30%. This has allowed us to invest more of the cost savings in transportation, so we can source more low-cost foam from remote areas and further expand our production!”
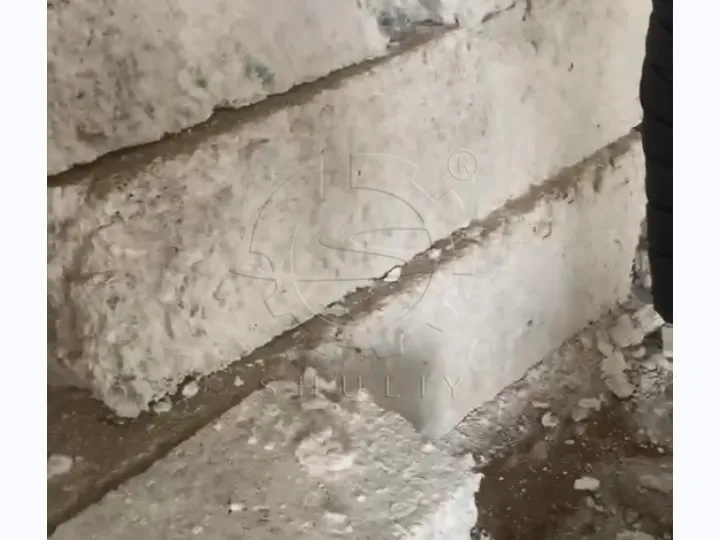
Conclusion
Congratulations to Mr. Ifeanyi Bello for successfully enhancing space utilization and foam recovery efficiency with the Shuliy styrofoam compressors! Shuliy’s cost-effective EPS recycling equipment is a vital component in the cycle of improved space efficiency, better purchasing strategies, and enhanced production continuity. If you are interested in learning more, please feel free to contact us!